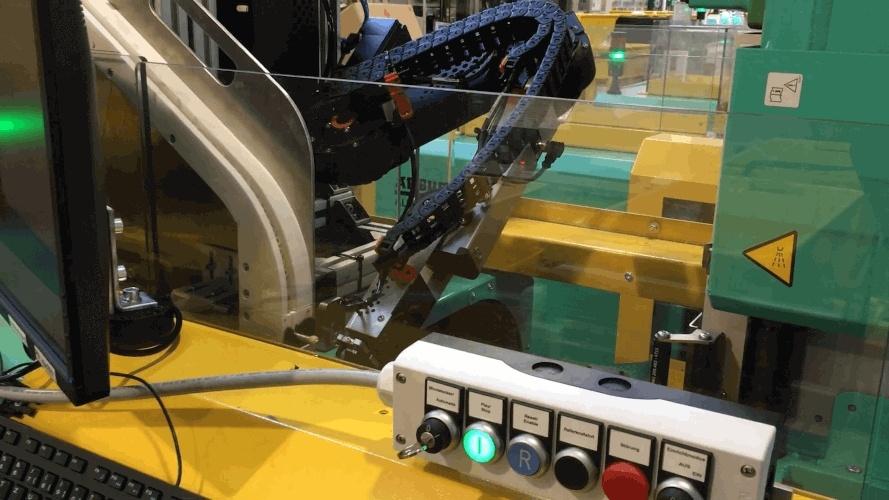
igus robolink - pick & place in a three-shift operation
Hardware Price:
ROI
6
months
accuracy
0.5
mm
project cost
22,000
GBP
Cost-Effective Automation with robolink: Optimizing Injection Molding Production
Automation is critical for industrial companies facing increasing pressure to optimize workflows and maintain consistency. At igus, the robolink robotic arm has been integrated into an injection molding system to automate the insertion of plastic spherical caps, with precision measured at 0.5 mm and a speed of 0.25 m/s. By replacing manual processes with robotics, productivity has increased alongside product quality, while employees are relieved from monotonous tasks.
What is the Application?
Used in injection molding, the robolink robot automates the placement of spherical caps into machines, executes precision overmolding, and repeats the process efficiently over three shifts to produce 250,000 parts annually.
What are the Advantages of the Solution?
Enhanced Productivity: Operates continuously, even during employee breaks.
Improved Quality: Reduces errors caused by fatigue during repetitive manual work.
Low-Cost Investment: Payback achieved within around four months.
What are the Advantages of the Robot?
The robolink arm offers affordable and efficient performance:
Ease of Use: Plug-and-play setup with intuitive controls requiring minimal training.
Low Maintenance: Triboplastics ensure dry operation, eliminating lubricant costs.
Flexibility: Employees can teach new movement sequences without programming expertise.
Empowering SMEs through Accessible Automation
The robolink robotic arm proves that automation is achievable even for small and medium-sized enterprises at low cost and risk. With easy-to-operate technology, reduced maintenance expenses, and employee-centric training, igus demonstrates how robotics can boost productivity without sacrificing the workforce’s role—making automation both economical and empowering.
3 Components